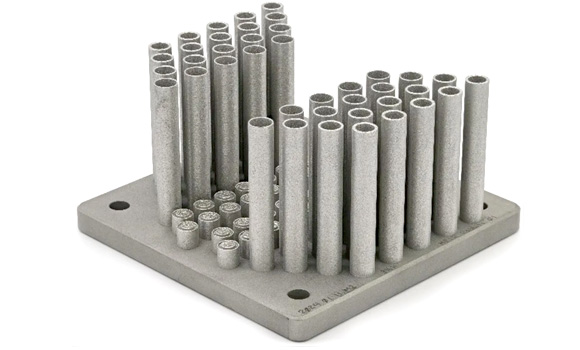
Additively manufactured steel capsules successfully tested in nuclear reactor environment at ORNL
How did your country report this? Share your view in the comments.
Diverging Reports Breakdown
3D-printed steel endures month-long trial in extreme nuclear reactor
These capsules, made from 316H stainless steel, are designed to hold sample materials during irradiation experiments. Acting as both pressure and containment barrier, the capsules help researchers examine how different materials respond to intense nuclear conditions.
Printing parts, testing limits
Acting as both pressure and containment barrier, the capsules help researchers examine how different materials respond to intense nuclear conditions, which is a critical part of qualifying components for reactor use.
To manufacture the capsules, Oak Ridge’s Manufacturing Demonstration Facility used a laser powder-bed fusion system to 3D print the stainless steel parts.
This specific type of steel is valued for its high-temperature strength, corrosion and radiation resistance, and proven nuclear-grade performance.
Once printed, the capsules were assembled and qualified by ORNL’s Irradiation Engineering group before undergoing a month-long irradiation period at HFIR.
The capsules were removed fully intact, marking a significant step in demonstrating that additively manufactured components can meet the stringent safety standards required in nuclear environments.
Rabbit capsule: US 3D-prints 1st nuclear reactor part, makes history
Researchers at ORNL have successfully designed, 3D printed, and tested a crucial component for their High Flux Isotope Reactor. This is the first time additive manufacturing has been used to create and qualify a component for use in
This component, known as a “rabbit capsule,” is a small container used to hold experimental materials during irradiation testing.
This is the first time additive manufacturing has been used to create and qualify a component for use in a nuclear reactor.
“Specimen capsules, commonly referred to as rabbit capsules, are used in nuclear fuels and materials research to hold experiments undergoing irradiation in a test reactor,” explained the US Department of Energy in a press release.
3D-printed steel capsules endure nuclear reactor testing
3D-printed steel capsules endure nuclear reactor testing at Oak Ridge National Laboratory. The capsule provides a pressure and containment barrier for the experiment, which is a critical safety feature. This achievement marks an important step in demonstrating that additively manufactured components can meet the rigorous safety standards required in nuclear applications. Additive manufacturing, or 3D printing, could streamline the development of experimental capsules, significantly reducing the cost and time associated with producing these components, ultimately driving greater innovation in nuclear science and technology. The capsules underwent a month-long irradiation in the reactor and were removed fully intact. They are made from 316H stainless steel that provides high-temperature strength, corrosion and radiation resistance, proven nuclear-grade performance and weldability.
ORNL researchers used a laser powder-bed system at the lab’s Manufacturing Demonstration Facility to 3D print 316H stainless steel capsules for use in irradiation experiments. The capsule provides a pressure and containment barrier for the experiment, which is a critical safety feature. Credit: ORNL, U.S. Dept. of Energy
The Department of Energy’s Oak Ridge National Laboratory set a new milestone in nuclear component innovation, successfully testing two 3D-printed stainless steel experimental capsules at the lab’s High Flux Isotope Reactor, or HFIR.
This achievement marks an important step in demonstrating that additively manufactured components can meet the rigorous safety standards required in nuclear applications.
These capsules are used to hold sample materials during irradiation experiments, allowing researchers to test how those materials might respond in a nuclear reactor. The capsule provides a pressure and containment barrier for the experiment, which is a critical safety feature.
An ORNL team used a laser powder-bed system at the lab’s Manufacturing Demonstration Facility, or MDF, to 3D print the 316H stainless steel capsules. This type of steel is being evaluated because it offers high-temperature strength, corrosion and radiation resistance, proven nuclear-grade performance and weldability needed for safe, durable use in reactor environments.
The team then assembled and qualified the capsules to be inserted into HFIR by ORNL’s Irradiation Engineering group. The capsules underwent a month-long irradiation in the reactor and were removed fully intact. This demonstration sets the stage for future nuclear component designs to be produced using additive manufacturing.
“As we demonstrate the reliability of these printed components, we’re looking at a future where additive manufacturing might become standard practice in producing other critical reactor parts,” said Ryan Dehoff, director of the MDF at ORNL.
HFIR provides one of the world’s highest neutron flux environments, allowing researchers to test and qualify fuels and materials under conditions such as a nuclear reactor. Fabricating and qualifying experimental capsules to irradiate fuel and material samples is a costly and time-consuming process, demanding custom materials and designs.
Additive manufacturing, or 3D printing, could streamline the development of experimental capsules, significantly reducing the cost and time associated with producing these components, ultimately driving greater innovation in nuclear science and technology.
The assembled capsule is made from 316H stainless steel that provides high-temperature strength, corrosion and radiation resistance, proven nuclear-grade performance and weldability. Credit: ORNL, U.S. Dept. of Energy
“The nuclear materials and fuels research communities are being asked to qualify advanced reactor technologies to survive very harsh conditions. Additive manufacturing will expand my group’s toolset to develop innovative experiments to support this critical need,” said Richard Howard, a group leader in the Nuclear Energy and Fuel Cycle Division at ORNL.
This work was sponsored by the DOE Office of Nuclear Energy’s Advanced Materials and Manufacturing Technologies program. HFIR is a DOE Office of Science user facility. MDF, supported by DOE’s Advanced Materials and Manufacturing Technologies Office, is a nationwide consortium of collaborators working with ORNL to innovate, inspire and catalyze the transformation of U.S. manufacturing.
UT-Battelle manages ORNL for the Department of Energy’s Office of Science, the single largest supporter of basic research in the physical sciences in the United States. The Office of Science is working to address some of the most pressing challenges of our time.
ORNL creates first 3D printed rabbit capsule for use in HFIR test reactor
Researchers working on additive manufacturing technology for nuclear energy applications have designed, 3D printed, and tested a specimen capsule for the High Flux Isotope Reactor. This marks the first successful demonstration of additive manufacturing in creating and qualifying such components for use in a nuclear reactor. Researchers aim to leverage the geometric flexibility of 3D printing to create more complex and innovative components that are otherwise difficult to fabricate. The U.S. Department of Energy’s Advanced Materials and Manufacturing Technologies program supports the project, which is dedicated to accelerating the commercialization of new materials and manufacturing techniques.
According to a report by the US DoE, Oak Ridge National Laboratory (ORNL) researchers working on additive manufacturing technology for nuclear energy applications have designed, 3D printed, and tested a specimen capsule, commonly known as a “rabbit capsule,” for the center’s High Flux Isotope Reactor (HFIR). This marks the first successful demonstration of additive manufacturing in creating and qualifying such components for use in a nuclear reactor.
Rabbit capsules are essential for nuclear fuels and materials research, serving as containers for experimental materials undergoing irradiation in test reactors. Using a laser powder bed fusion process, ORNL fabricated a stainless-steel capsule, which was assembled, loaded with experimental materials, and sealed. This capsule was subjected to HFIR’s intense neutron flux environment for nearly a month and successfully endured extreme conditions, showcasing the viability of additive manufacturing for nuclear applications.
Richard Howard, the group lead for irradiation engineering at ORNL, highlighted the importance of this achievement by stating that it represents a major step forward in demonstrating how additive manufacturing can develop and qualify specialized components that traditional machining cannot produce.
The adoption of additive manufacturing for nuclear applications offers multiple advantages. It enables intricate and unique designs that are difficult to achieve using conventional methods. It also reduces production time and costs while allowing for rapid prototyping and easier integration of design modifications. Ryan Dehoff, Manufacturing Demonstration Facility Director at ORNL, expressed optimism about the future of this technology, suggesting that it might become standard practice for producing critical reactor parts as its reliability continues to be demonstrated.
After successful testing, ORNL plans to conduct post-irradiation evaluations of the capsule this winter. These evaluations will provide deeper insights into how the additively manufactured component performed under the challenging conditions of the reactor.
This marks yet another small step in ORNL’s research toward the exploration of 3D printing in nuclear energy with strict material composition, design, and qualification standards. Previous experiments saw the 3D printing of an entire small nuclear reactor and, most recently, for reducing inspection time for 3D printed nuclear parts and components. Researchers aim to leverage the geometric flexibility of additive manufacturing to create more complex and innovative components that are otherwise difficult to fabricate.
The U.S. Department of Energy’s Advanced Materials and Manufacturing Technologies program supports the project, which is dedicated to accelerating the commercialization of new materials and manufacturing techniques through research, demonstration, and deployment.