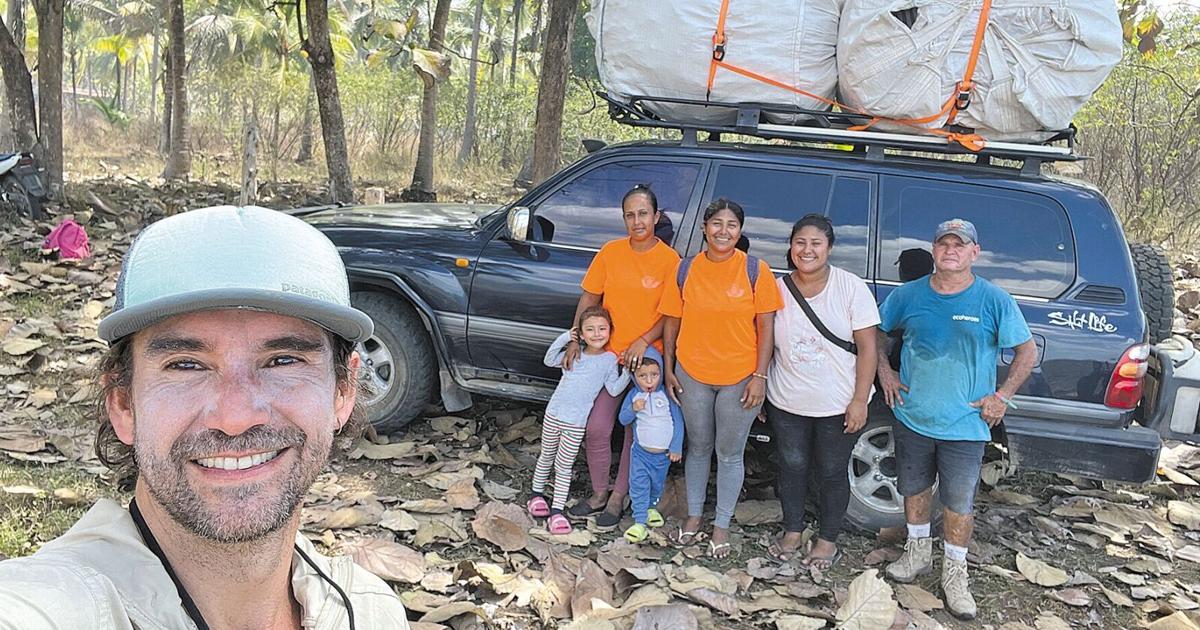
Cementing a New Future for Plastic Waste
How did your country report this? Share your view in the comments.
Diverging Reports Breakdown
Cementing A Circular Future
New EU Packaging and Packaging Waste Regulation (PPWR) in effect since February 11, 2025. By 2040, packaging waste should be significantly reduced, and from 2030 onward, stricter recyclability standards will apply. Now is the time for the cement and building materials industry to rethink its packaging to avoid costly adjustments tomorrow and turn compliance into a competitive advantage. Compliance not only safeguards businesses from regulatory risks but also strengthens brand reputation, cost efficiency, and environmental impact. Fortunately, there are already different solutions from the sack kraft paper and paper sack industry in place that can function as a role model for future expansion. They all show that collaboration along the value chain is key when it comes to establishing an efficient circular system. Read the full article and the rest of the June issue of World Cement by registering today for free!
One environmental policy tool impacting the cement industry is ‘extended producer responsibility,’ or EPR. It requires producers of cement and building materials to take responsibility for the environmental impact of their products throughout their entire lifecycle, from production and usage to disposal. Among other things, manufacturers will have to ensure that their packaging is recyclable and to finance the collection, sorting, and recycling through EPR fees. EPR obligations for packaging derive from broader EU legislation. With the new EU Packaging and Packaging Waste Regulation (PPWR) in effect since February 11, 2025, the requirements are becoming even stricter. By 2040, packaging waste should be significantly reduced, and from 2030 onward, stricter recyclability standards will apply. A crucial aspect for manufacturers: starting in 2028, EPR fees will be adjusted based on how recyclable their packaging is. This so-called recyclability performance will be defined by delegated acts.
Future-proofing cement packaging
With these evolving regulations, how can the cement and building materials industry ensure its packaging remains compliant? And more importantly, how does this effort translate into business advantages? The answer lies in innovation. Now is the time for the cement and building materials industry to rethink its packaging to avoid costly adjustments tomorrow and turn compliance into a competitive advantage. Compliance not only safeguards businesses from regulatory risks but also strengthens brand reputation, cost efficiency, and environmental impact.
Paper cement sacks: perfectly recyclable
Industrial paper sacks are widely used for cement and other building materials. In 2024, more than 3 billion sacks were placed on the European market. While Germany and Spain already have established providers for paper sack collection and recycling, there is no unified, Europe-wide system in place. As a result, paper sacks are often collected within a mixed stream of paper packaging for recycling. Therefore, ensuring their compatibility with standard mill recycling processes is essential. A recent lab study, commissioned by EUROSAC and CEPI Eurokraft, found that both used and unused cement paper sacks – with or without plastic film layers – are fully recyclable under the conditions of standard high-volume recycling mills, as per industry standard. Furthermore, the study revealed that the inclusion of sack kraft fibres in the recovered paper fibre mix enhances the quality and strength of the recycled material. It may also bring processing benefits as it improves yield and lowers drying energy requirements when used in paper manufacturing.
Improving design for recyclability
Ensuring recyclability plays a very crucial role with the new legislation. All packaging with a recyclability performance that scores lower than 70% will be banned from the market by 2030. By 2038, the recyclability performance score must be at least 80%. Adding to that, the recyclability performance score will influence EPR fees. They will be adjusted according to the environmental performance of materials and the recyclability grade. To equip paper sack fillers, sack kraft paper producers, and paper sack converters with insights into how material and design choices impact recyclability, EUROSAC and CEPI Eurokraft have published design for recyclability guidelines. These guidelines enable producers to maximise the recyclability of the paper sacks they place on the market. Beyond achieving a strong recyclability performance score, by 2035, all packaging must be recycled at scale. This means that collection, sorting, and recycling systems must be fully established and operational across all relevant regions in Europe. Fortunately, there are already different solutions from the sack kraft paper and paper sack industry in place that can function as a role model for future expansion. They all show that collaboration along the value chain is key when it comes to establishing an efficient circular system.
Enjoyed what you’ve read so far? Read the full article and the rest of the June issue of World Cement by registering today for free!
Shree Cement and RSPCB Launch Plastic Waste Collection Centres in Jaipur on World Environment Day 2025Shree Cement and RSPCB join hands to launch plastic waste centres in Jaipur
The initiative aims to create a sustainable model for urban plastic waste management in Rajasthan. The four centres will serve as collection hubs for gathering plastic waste, which will then be transported to Shree Cement’s integrated cement plants in Ras, Beawar and Nawalgarh for co-processing. This method involves using non-recyclable plastic waste as an alternative fuel in cement kilns—a scientifically recognised and environmentally responsible disposal method.
The initiative aims to create a sustainable model for urban plastic waste management in the state. The four centres will serve as collection hubs for gathering plastic waste, which will then be transported to Shree Cement’s integrated cement plants in Ras, Beawar and Nawalgarh for co-processing. This method involves using non-recyclable plastic waste as an alternative fuel in cement kilns—a scientifically recognised and environmentally responsible disposal method.
Mr. Neeraj Akhoury, Managing Director, Shree Cement, said, ““At Shree Cement, we believe in turning commitment into action. With this initiative, RSPCB empowers us to support Rajasthan’s environmental goal by developing practical, scalable solutions to tacke the critical challenge of plastic waste in the cities. Together, we are working towards a more sustainable and responsible future. ”
Under this initiative, Shree Cement will operate and manage plastic waste collection centres. RSPCB will lead public awareness efforts, local engagement, and facilitate operational support. The initiative is part of Shree Cement’s Corporate Social Responsibility (CSR) programme and reflects the company’s continued focus on sustainability and environmental stewardship.
This initiative not only contributes to better waste management practices but also enhances Shree Cement’s engagement with local communities and regulatory bodies, reinforcing its role as a socially responsible and sustainability-driven organisation.
SM Prime: Creating infrastructure for plastic-free communities
According to the United Nations Environmental Programme (UNEP), the global production of plastics is forecasted to reach 1,100 million tonnes by 2050. SM Prime is pursuing a group-wide strategy to comply with the Department of Environment and Natural Resources (DENR)’s EPR Act of 2022. The property arm of the SM group aims to create the needed infrastructure that will help support and maintain plastic waste management strategies. The annual International Coastal Clean-up (ICC), supported by SM Cares, continues to empower volunteers to take part in this global effort for a record-breaking initiative. The SM Hotels and Conventions Corporation (SMHCC) has long since eliminated SUPs from all properties in support of the UNEP’s campaign to phase them out. Since 2019, the SMX Convention Centers’ guidelines promote environmentally friendly alternatives to cutlery, bamboo or starch-based waste management practices to minimize waste generation. Through enhanced waste management systems, effective waste segregation, and proactive community effort, SM Prime aims to divert a greater proportion of plastic waste away from landfills.
As one of Southeast Asia’s largest integrated property developers, SM Prime Holdings, Inc. (SM Prime) remains committed to creating thriving, sustainable cities.
With a waste-free future as part of its environmental strategy, SM Prime encourages the observation of International Plastic-free Day on May 25 and its call to rethink single-use plastics (SUP) for one day. Moreover, SM Prime celebrates the group-wide strides made to support the Extended Producer Responsibility (EPR) Act of 2022.
A group-wide movement for the EPR Law
The SM group, working with its Producer Responsibility Organization (PRO), Philippine Alliance for Recycling and Materials Sustainability (PARMS), is pursuing a group-wide strategy to comply with the Department of Environment and Natural Resources (DENR)’s EPR Act of 2022.
Formally known as Republic Act 11898, the EPR law requires companies to take responsibility for the recovery of their plastic packaging products and to pursue waste management programs.
Acknowledging the challenges and realities for businesses and on-ground operations through its EPR working group committee, the SM group commits to a plan of action in reducing and recovering its plastic footprint within the given five-year period, sharing alternatives and new technologies to respond to the growing global crises, and establishing partnerships with government agencies and other private institutions.
As the property arm of the SM group, SM Prime’s commitment to a waste-free future aims to create the needed infrastructure that will help support and maintain plastic waste management strategies.
Crucial to waste recovery efforts, SM Prime equips its properties with a Materials Recovery Facility (MRF), and standardized waste segregation and management practices to help reduce the amount of waste sent to landfills. A joint venture with a Japanese environmental solutions company, the SM GUUN Environmental Company, Inc. (SGECI), converts non-recyclable waste into cement fuel or “fluff fuel” for eco-conscious cement companies like APO Cement, Holcim, and Taiheiyo Cement, as part of its “co-processing” practice.
Beyond compliance
SM Prime continues with its established programs such as the nationwide Trash to Cash recycling market. Since 2007, it has been one of SM Supermalls’ flagship programs that continues to be more relevant given the times.
Activating the SM malls to help their communities with sorted plastic waste, Trash to Cash incentivizes the exchange of recyclables to provide a venue for plastic recovery. Fifteen SM Plastic Waste Collection sites likewise serve as drop-off points for clean, empty, and dry plastics. In addition, the Solid Waste Action Program (SWAP) reverse vending machines at SM Megamall and SM Mall of Asia enable the diversion of aluminum cans and polyethylene terephthalate bottles (PET), which are considered high-value plastic products.
The annual International Coastal Clean-up (ICC), supported by SM Cares, continues to empower volunteers to take part in this global effort for a record-breaking initiative. In 2024 alone, SM Cares helped mobilize 23,000 employees, students, and various communities that joined nationwide volunteer efforts to remove trash from the world’s beaches and waterways.
Aiming for a waste-free future
Reduction is always the best option. The SM Hotels and Conventions Corporation (SMHCC) has long since eliminated SUPs from all properties in support of the UNEP’s campaign to phase them out. Pico Sands Hotel was also one of the first hotels to sign with the World-Wide Fund for Nature Philippines (WWF) in their Ayoko Na Sa Plastic Campaign in 2018.
SMHCC has successfully replaced all single-use amenities, such as high-density polyethylene (HDPE) shampoo and shower gel bottles, and PET water bottles in all its hotel rooms. Since 2019, as part of the SMX Convention Centers’ guidelines to promote sustainable events management practices, bamboo or starch-based environmentally friendly alternatives to replace plastic cutlery are encouraged to minimize waste generation.
Working collectively as a group to reduce the effects of the plastic waste crises creates a bigger impact at a greater scale. Through enhanced waste management systems, effective waste segregation practices, and proactive community effort, SM Prime aims to successfully divert a greater proportion of plastic waste away from landfills.
“Our work is never done. There are new technologies, innovative solutions, and more avenues for collaboration to look forward to in making the EPR Act work for our communities,” said Engr. Liza Silerio, Vice President for Corporate Compliance and Program Director of SM Cares for Environment. “But we all have a role to play–it is every individual’s responsibility to create a waste-free future.”
ADVT.
This article is brought to you by SM Prime.
RockFuel: Reinventing cement and building a climate-positive future
RockFuel is redefining cement, turning concrete infrastructure and construction into a solution for global decarbonisation that is True Net Zero. The cement industry is forecast to grow from $316.3bn in 2020 to over $463bn by 2026, driven by infrastructure investment, population growth, and urbanisation. As nations introduce stricter carbon policies, the demand for climate-positive materials is rapidly increasing. RockFuel’s closed-loop kiln, powered entirely by renewable energy sources – including solar, wind, hydroelectric, or energy recovered from other RockFuel processes – collects over 500 cubic metres of hot CO₂ per cubic metre of limestone rock processed, storing it in a dedicated tank for reuse. This multi-output system ensures minimal waste and creates new revenue opportunities, enhancing commercial appeal for investors and manufacturing partners. The company is now seeking strategic partnerships with cement producers, lime producers, and lime-numbers producers to ensure their long-term operations and operations are decarbonised and ready for global adoption.
As the world intensifies its efforts to combat climate change, industries under mounting scrutiny are being challenged to innovate or become obsolete. Cement production, responsible for approximately 8% of global CO₂ emissions, is a prime target for transformation. Now, a pioneering solution from UK-based company RockFuel promises to revolutionise the sector: a Carbon Negative cement process that doesn’t just lower emissions – it reverses them.
With a patented closed-loop manufacturing system that produces ‘carbon neutral CO₂’, RockFuel’s approach offers a scalable, economically viable, and truly climate-positive alternative to conventional cement. This development marks a significant milestone in sustainable construction and positions RockFuel as a key player in the decarbonisation of the global construction materials industry.
Cementing a new future with carbon capture
At the heart of this innovation is RockFuel’s Carbon Neutral Lime Kiln, a high-efficiency system that produces quicklime (CaO) while capturing the CO₂ released during the process. Traditional cement kilns vent this CO₂ directly into the atmosphere. RockFuel’s closed-loop kiln, powered entirely by renewable energy sources – including solar, wind, hydroelectric, or energy recovered from other RockFuel processes – collects over 500 cubic metres of hot CO₂ per cubic metre of limestone rock processed, storing it in a dedicated tank for reuse.
The captured CO₂ is not simply stored or sequestered, it is reintegrated into the production cycle in a novel way, forming the basis of RockFuel’s Carbon Negative cement solution. By closing the loop and incorporating carbon capture at the manufacturing stage, RockFuel offers a blueprint for next-generation industrial processes.
From emission source to carbon sink
In RockFuel’s Carbon Neutral cement process, the cement begins as quicklime (CaO – Calcium Oxide), produced in the company’s kiln from CaCO3, powered by Carbon Neutral energy. It is then blended with clay to create cement, while the captured CO₂ undergoes electrolysis, using excess energy from the system, which contributes towards a carbon-neutral process. This yields solid carbon and carbon-neutral oxygen, both valuable industrial byproducts.
Solid carbon can be used in advanced materials such as carbon fibre and graphene, while oxygen finds applications in steel manufacturing, wastewater treatment, medical technology, and the chemical industry. This multi-output system ensures minimal waste and creates new revenue opportunities, enhancing commercial appeal for investors and manufacturing partners.
Crucially, when RockFuel’s cement is used in construction and the resultant concrete begins to cure, it absorbs additional atmospheric CO₂, turning infrastructure into long-term carbon sinks. This makes the product not just Carbon Neutral, but Carbon Negative across its lifecycle — a critical differentiator in the race toward global decarbonisation in the built environment and infrastructure projects worldwide. While some governments do not generally accept the figures for this natural carbon curing effect, the RockFuel Carbon Negative Cement Process includes a very small fraction of calcium oxide used in ocean projects, where around double the amount of CO₂ is absorbed, which ensures the whole process is Carbon Negative.
Meeting global market demands
The cement industry is forecast to grow from $316.3bn in 2020 to over $463bn by 2026, driven by infrastructure investment, population growth, and urbanisation across all continents. As nations introduce stricter carbon policies, the demand for climate-positive materials is rapidly increasing.
While the Asia-Pacific region continues to dominate production volumes, North America and Europe are leading in regulatory pressure and innovation-driven sustainability strategies. Both public and private sectors, governments, investors, and project developers are searching for materials that offer verifiable carbon reductions without compromising performance, compatibility, or cost-effectiveness. RockFuel’s solution addresses all three.
The chemical properties of the cement remain identical to traditional formulations, meaning it can be used in existing applications, such as poured concrete or precast components, without altering construction methods or regulatory standards. This makes it an ideal drop-in alternative for infrastructure projects, from transport networks to commercial buildings and renewable energy installations, such as the cement foundations for wind turbines and electricity transmission towers.
Verified, patented, and ready for global partnerships
RockFuel’s technology has undergone independent chemical engineering validation and financial modelling, demonstrating both technical feasibility and commercial viability. The company holds multiple international patents, with further applications pending, ensuring that this innovation is protected and ready for global licensing and industrial adoption.
The company is now seeking strategic partnerships with:
Cement, lime, concrete producers, and lime kiln manufacturers looking to decarbonise operations and ensure their long-term viability in a climate-positive world;
looking to decarbonise operations and ensure their long-term viability in a climate-positive world; Universities and research institutes interested in co-operating on materials science, industrial chemistry, or sustainability innovations, e.g. via Horizon Europe collaboration;
interested in co-operating on materials science, industrial chemistry, or sustainability innovations, e.g. via Horizon Europe collaboration; Government agencies focused on green infrastructure, industrial transition, a climate-positive built environment and clean energy policy;
focused on green infrastructure, industrial transition, a climate-positive built environment and clean energy policy; Impact investors and clean-tech funds seeking scalable, commercially sound climate solutions that are profitable and ready for upscaling.
Building toward a truly sustainable planet
The cement industry has long been seen as incompatible with true sustainability goals. RockFuel is overturning that perception. With a technology that turns CO₂ emissions into valuable outputs and cement-based infrastructure into carbon sinks, RockFuel is not just reducing the impact of cement, it is transforming it into one of the most climate-positive building materials available.
This innovation has the potential to reframe how construction contributes to environmental targets, no longer as a reluctant emitter, but as an active agent in atmospheric carbon reduction. It allows built environments to become tools in the fight against climate change, offering governments and industries a real, scalable way to build better and cleaner.
As the world races to decarbonise, RockFuel offers a ready-to-implement ‘Real Zero’ solution for one of the hardest-to-abate sectors. For policymakers, researchers, and industry leaders, it represents a beacon of what’s possible when circular design, energy transition, and practical innovation converge.
Please note, this article will also appear in the 22nd edition of our quarterly publication.
Future-proof pathways to cleaner cement
Carbon capture, utilisation and storage (CCUS) is expected to play a leading role in the decarbonisation of cement. The Global Cement and Concrete Association (GCCA) has positioned CCUS as a cornerstone of its roadmap to net-zero. The Leilac technology is an emergent process technology that aims to provide the Best Available Technique for the calcination step in existing cement plants. The technology is being designed to enable multiple advantages, including the low-cost capture of unavoidable CO 2 emissions, lower and even optimised energy costs, new revenues, and enhanced productivity. This technology aims to deliver its ability to deliver two potential benefits: minimising energy costs and delivering continuous heat whilst delivering stable production costs. First, it could deliver the ability to fully deliver electric calcination, which could deliver potential benefits of minimising fuel emissions entirely. Second, it can deliver continuous heat, delivering continuous production costs, whilst delivering continuous energy costs to maintain stable production. This could deliver possible benefits of low-carbon production.
2 days ago Source: Calix Limited
Carbon capture, utilisation and storage (CCUS) is expected to play a leading role in the decarbonisation of cement. The Global Cement and Concrete Association (GCCA) has positioned CCUS as a cornerstone of its roadmap to net-zero, with carbon capture delivering the highest share of emissions reductions, against all other measures, by 2050.1 However, for cement manufacturers now evaluating business cases for CCUS, early adoption remains fraught with commercial uncertainty.
Conventional carbon capture technologies aimed at cement are designed as discrete, single purpose solutions – they capture CO 2 , at cost. The potential value created by these technologies is heavily dependent on enabling factors within the broader CCUS value chain: transport and storage infrastructure, public subsidy, regulatory support and market incentives. An end-to-end CCUS project involves a lot of moving parts, raising project risk and uncertainty.
To scale carbon capture in cement, manufacturers need optionality. A cement plant needs flexibility in when and how it will deploy CCUS. Technologies should offer multiple sources of value to the cement plants that adopt them, and be adaptable to the complex and evolving challenges that the industry faces. Ideally, a manufacturer would draw on multiple levers over time to decarbonise economically.
The Leilac technology offers a multi-pronged approach to decarbonisation in cement. Leilac’s core indirect heating process is adaptable to the unique and often contrasting needs of individual cement plants. Leilac’s ‘capture-ready’ capability could offer the cement and lime industries a de-risked approach to decarbonisation.
Indirect heating – a future-proof solution The Leilac technology is an emergent process technology that aims to provide the Best Available Technique for the calcination step in existing cement plants. Proven at a multi-tonne-per-hour rate at the Leilac-1 pilot in Belgium, the Leilac process utilises a unique indirect heating method to calcine limestone or cement raw meal. The technology is being designed to enable multiple advantages, including the low-cost capture of unavoidable CO 2 emissions, lower and even optimised energy costs, new revenues, and enhanced productivity. For cement plants navigating changing market conditions, indirect heating could provide flexible, future-proof strategies for low-carbon and low-cost cement production. The Leilac technology is, in part, a carbon capture solution, but it is also an innovative cement production process. The reduced operating costs and new revenues that indirect heating may unlock are designed to create immediate business cases for technology adoption. Importantly, these benefits are not contingent on the immediate availability of a CCUS value chain, public subsidy, or other policy incentive. Not only would this support the deployment of capture-ready plants, but it could decouple the deployment of carbon capture technologies from carbon transport and storage infrastructure, thereby reducing project complexity and risk.
How does it work? Figure 1: The Leilac technology: A schematic of the indirect heating process.
In conventional cement and lime calcination, unavoidable process CO 2 emissions become entrained within flue gases, before being routed to the stack and released into the atmosphere. The CO 2 released from this process accounts for between 60 and 65% of a cement or lime plant’s facility-wide CO 2 emissions. In contrast, indirect heating works by keeping the released process CO 2 separate from flue gases and air. The heat source and the calcination process are physically isolated from one another via an inner alloy tube. The raw material is fed to this inner tube, whilst a combustion system and/or an electricity source externally heats the tube’s walls. The released CO 2 is then routed to an independent offtake, at high purity (proven at 98%), ready for use or storage. This CO 2 offtake stream can be either offline or online, depending on the availability of downstream carbon management infrastructure and market incentives.
Fuel switching, energy flexibility and near-term benefits Leilac’s unique indirect heating configuration creates a high degree of flexibility over the energy sources that can be used to drive the calcination reaction. The Leilac-1 pilot is powered by natural gas heating. The Leilac-2 demonstration plant is designed to enable near full use of lower-cost, lower carbon alternative fuel. Multiple operational pilot projects have proven the technology’s ability to deliver fully electric calcination, which could avoid fuel emissions entirely.
Figure 2: Multiple pilots have demonstrated calcination by indirect heating across various scales and energy sources.
In its next generation of designs, Leilac is developing its ability to deliver hybrid-fuel operations. This technology innovation aims to enable operators to dynamically switch between energy sources – whilst delivering continuous heat to maintain stable production. This could deliver two potential benefits. First, producers could minimise energy costs. Hybrid heating is designed to respond to daily and seasonal energy price fluctuations, empowering producers to switch to the lowest cost of energy locally available. For example, hybrid-fuel operations may enable a cement plant to capitalise on periods of low or negatively priced electricity, while remaining protected from periods of high electricity prices or unexpected shocks to fuel markets. In short, it is designed to enable flexible and optimised energy strategies that maximise the opportunities volatile markets present, whilst mitigating risks. Second, producers could unlock new revenues. The potential of a hybrid-fuelled technology to rapidly increase or decrease its electricity use makes it well suited for grid balancing activities. The electrical baseload introduced by a hybrid Leilac plant would create significant a source of demand-side flexibility. This energy flexibility could be provided as a balancing reserve to regional power grids and create a valuable new revenue stream for cement plants. Dynamic fuel switching may therefore deliver both immediate economic benefits and reduced carbon emissions. At the same time, it provides future-proof optionality for energy inputs and process emissions capture. Navigating CCUS uncertainty “Prediction is very difficult, especially about the future.” – Niels Bohr (physicist, Nobel laureate). In the conventional CCUS business case, the value created by capturing CO 2 from cement is contingent on a number of enabling factors, both now and into the future. However, the magnitude and timing of these future enablers remains somewhat uncertain. In 2024, The EU’s Industrial Carbon Management Strategy mapped a preliminary outline of a pan-European CCUS infrastructure network (figure 1). In 2025, the EU Commission allocated €250 million to support the initial stages of its development2 However, such infrastructure is likely to take many years to construct and commission. Although emissions trading schemes and other carbon pricing mechanisms continue to grow in both reach and value across the globe3,4, recent economic downturns have led to carbon price volatility, adding uncertainty to the near-term value decarbonisation projects can expect to unlock from this incentive.5 Conventional CCUS technologies fail to offer protection against the types of commercial uncertainties outlined above. Ideally, decarbonisation solutions aimed at cement will be more flexible and multi-purposed, providing strong benefits to producers in the near term and across divergent future scenarios.
Figure 3: Network of potential carbon transport routes (by 2040). Source: European Commission(2024) – Shaping the future CO2 transport network for Europe.
The capture-ready approach By delivering immediate business cases for technology adoption that are independent of carbon pricing or downstream carbon management infrastructure, Leilac aims to deploy ‘capture-ready’ installations. Such an approach could offer significant advantages over the typical end-to-end CCUS business case.
A capture-ready cement plant could gain first-mover advantage in the CCUS value chain Traditional CCUS projects face a chicken and egg dilemma. The commercial viability of conventional carbon capture deployment depends on the availability of downstream transport and storage infrastructure. However, the development of carbon management infrastructure is dependent on there being sufficient carbon to manage. Leilac’s capture-ready approach aims to solve this dilemma by providing a de-risked, first steps approach towards CCUS network integration for cement. CCUS infrastructure could expand in the direction of capture-ready cement manufacturers. Meanwhile, plants could benefit from Leilac’s other advantages whilst they wait for said infrastructure to be constructed. This capability is in lockstep with the recently announced EU Carbon Management Strategy. “Early adopters, such as CO 2 capture and storage project developers, could play a vital role in shaping the CO 2 transport network. Their location, capacity and start date will influence the mapping and capacities of the transport routes. This, in turn, is expected to draw subsequent projects to use these routes to minimise costs.” – Joint Research Centre: European Commission (2025)6 Leilac’s capture-ready capabilities could be similarly applied to the expansion of North American CCUS infrastructure for cement. In the U.S., many cement plants can be grouped into distinct, geo-spatial clusters. The proximity of multiple plants suggests that the cement industry could play a leading role in CCUS network expansion. “If the cement industry leads industrial CCUS deployment, spatial analysis can identify carbon-hubs made of the nearest industrial neighbours to the pipeline to significantly reduce systems costs”
– MIT Concrete Sustainability hub (2024)7
A capture-ready cement plant could gain a competitive edge in the emerging carbon market Switching to lower carbon fuels can reduce emissions and ensure producers avoid carbon liabilities in the near term. The option to embark on low-cost CCUS has the potential to unlock deep decarbonisation, which may in turn deliver economic access to market incentives such as tax credits and emissions trading schemes.8 Carbon abatement can become a source of revenue.