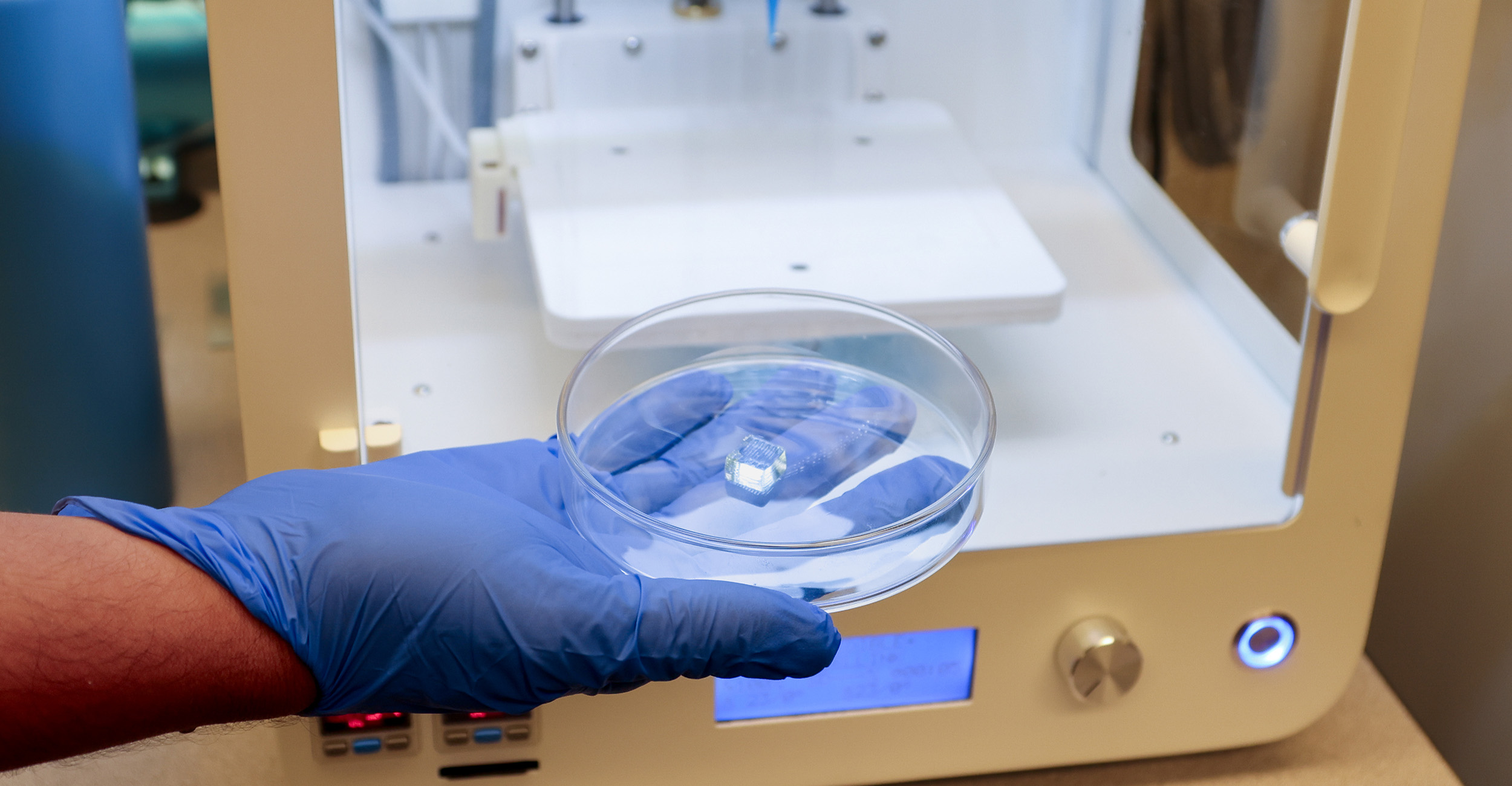
OSU research explores collaborative biofabrication for personalized health care
How did your country report this? Share your view in the comments.
Diverging Reports Breakdown
OSU research explores collaborative biofabrication for personalized health care
OSU research explores collaborative biofabrication for personalized health care. Project represents a significant step forward for digital manufacturing and biomanufacturing at OSU and beyond. Tissue scaffolds for both soft and hard tissue regeneration will be bioprinted to demonstrate the broad applicability of the methodology in bioFabrication. The team is also working with the Army’s DEVCOM CBC to assess the scalability and feasibility of the approach in defense-related bioengineering settings. If successful, it could reduce manufacturing costs, accelerate treatment/product development timelines and ultimately increase access to advanced biofabRICated solutions. The research will leverage both computational and experimental testbeds already in place atOSU. The project will expand student opportunities. Three graduate students will work on the project, and undergraduate students will also have the chance to engage. From medical innovation to secure digital manufacturing, CEAT researchers are building a future where patient privacy and personalized care go hand in hand.
Media Contact: Desa James | Communications Coordinator | 405-744-2669 | desa.james@okstate.edu
A new Oklahoma State University research project is reimagining how patient-specific bioengineered products are designed and manufactured by developing a privacy-aware collaborative framework.
This new approach will enable knowledge sharing between biofabrication facilities without exposing sensitive patient or design data, aiming to reduce product development time and support mass personalization in additive biofabrication. Funded by the National Science Foundation, the project represents a significant step forward for digital manufacturing and biomanufacturing at OSU and beyond.
The research team is comprised of Drs. Akash Deep, Srikanthan Ramesh and Paritosh Ramanan, all professors for the School of Industrial Engineering and Management.
The challenge is one of both complexity and customization. 3D bioprinting, an emerging biofabrication technique and a form of additive manufacturing, involves 3D printing living cells and biomaterials to create custom tissue architectures. It is promising for patient-specific health care applications, including tissue engineering and disease modeling. Unlike traditional manufacturing, each bioprinted product is uniquely tailored to match an individual’s anatomy for regenerating lost or damaged tissue or to replicate a specific disease condition for research and therapeutic testing. However, this level of personalization requires substantial time and resources.
To meet this challenge, the CEAT team is building a decentralized learning framework that preserves patient data privacy while enabling biofabrication facilities to share and build on each other’s design and manufacturing strategies (i.e., similar to adapting a recipe), without having to start from scratch every time a new patient-specific product is needed.
At the heart of this approach is a novel collaborative design algorithm that facilitates knowledge transfer between manufacturing facilities, significantly reducing trial-and-error. Moreover, by using differential privacy techniques — a state-of-the-art data protection method that adds statistical “noise” to sensitive datasets — they can ensure that shared insights don’t compromise patient confidentiality.
“We’re not pulling private medical data into a central system,” Ramanan said. “Instead, we’re sending our algorithms to the data, deploying them directly to the printers where the information lives. That’s how we protect privacy while still enabling collaboration.”
Tissue scaffolds (i.e., biodegradable structures that support the regrowth of tissue inside the human body) for both soft and hard tissue regeneration will be bioprinted.
The research will leverage both computational and experimental testbeds already in place at OSU. These include physical testbeds at OSU-Tulsa and OSU-Stillwater that simulate two collaborating facilities, along with virtual ones that can simulate multiple printing centers working in tandem. The physical testbeds will validate the framework in real-world 3D bioprinting scenarios, while the virtual testbeds will test its scalability and privacy performance across a simulated network of facilities. Tissue scaffolds (i.e., biodegradable structures that support tissue regrowth inside the human body) for both soft and hard tissue regeneration will be bioprinted to demonstrate the broad applicability of the methodology in biofabrication.
The team is also working with the Army’s DEVCOM CBC (as part of its industry engagement efforts) to assess the scalability and feasibility of the approach in defense-related bioengineering settings. If successful, it could reduce manufacturing costs, accelerate treatment/product development timelines and ultimately increase access to advanced biofabricated solutions. More broadly, it addresses a key limitation in current biofabrication systems by enabling secure, distributed collaboration, laying the groundwork for a more connected and responsive manufacturing ecosystem.
In addition to its research impact, the project will expand student opportunities. Three graduate students will work on the project, and undergraduate students will also have the chance to engage.
From medical innovation to secure digital manufacturing, CEAT researchers are building a future where personalized care and patient privacy go hand in hand.